Advanced Techniques in Metal Stamping for Precision Production
As industries consistently demand finer tolerances and elaborate layouts in their metal components, the quest for advanced techniques in steel stamping has intensified. From the application of sophisticated multi-stage stamping processes to the assimilation of advanced automation technologies, the landscape of steel stamping is going through a profound makeover.
Advanced Multi-Stage Stamping Processes
Going over the complexities of innovative multi-stage marking processes discloses the advanced techniques employed in modern-day manufacturing methods. Metal Stamping. Multi-stage stamping is a complicated process that entails several steps to transform a level sheet of steel right into a final stamped product. Using modern dies, where various operations are performed at each phase of the stamping procedure, enables high accuracy and efficiency in the production of elaborate metal components
Throughout the initial phases of multi-stage marking, the flat metal sheet is fed into the marking press, where a collection of passes away are used to cut and form the product. Succeeding phases involve added forming, bending, and punching operations to more refine the component. Each stage is meticulously developed to build on the previous one, causing the development of intricate geometries with tight tolerances.
Advanced multi-stage marking processes require a high degree of know-how and precision to ensure the top quality and consistency of the stamped components. By using advanced equipment and tooling, suppliers can produce a wide variety of metal elements with efficiency and precision.
Precision Tooling Innovations
Accuracy tooling technologies have actually revolutionized the metal marking market, boosting effectiveness and quality in manufacturing processes. CNC systems allow for detailed styles to be converted directly right into tooling, making certain accuracy and repeatability in the stamping procedure.
Furthermore, the integration of sensors and real-time surveillance capacities in precision tooling has enabled suppliers to discover and deal with problems promptly, reducing downtime and reducing scrap rates. By incorporating wise technology right into tooling, operators can enhance specifications such as stress, speed, and placement during the marking operation, causing boosted item quality and increased productivity.
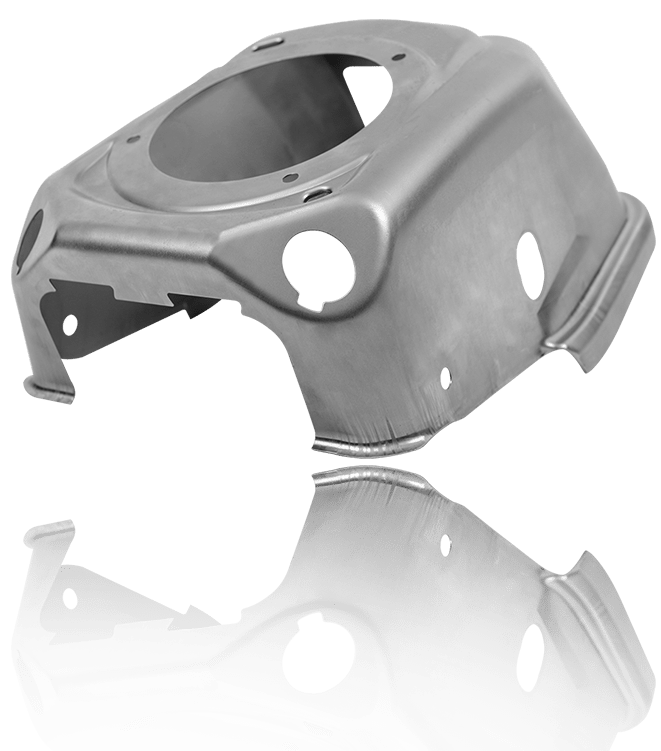
Automation in Metal Stamping
The development of accuracy tooling advancements in the steel marking market has led the way for substantial improvements in automation, changing the production landscape towards enhanced effectiveness and performance. Metal Stamping. Automation in metal stamping includes making use of innovative equipment and robotics to perform numerous tasks generally accomplished by human operators. This change in the direction of automation supplies various benefits, including enhanced accuracy, quicker production cycles, and decreased labor expenses
One secret aspect of automation in her response metal stamping is the application of computer system numerical control (CNC) systems, which enable precise control over the stamping procedure. CNC innovation enables the development of complicated and complex steel components with regular top quality. Additionally, automated systems can be programmed to run continuously, bring about greater outcome rates and much shorter lead times.
Moreover, automation enhances workplace safety by minimizing manual handling of heavy materials and lessening the danger of mishaps (Metal Stamping). As manufacturing industries proceed to welcome automation, the future of metal stamping holds great assurance for also greater performance and innovation
High-Speed Stamping Methods

Among the primary advantages of high-speed stamping strategies is the capacity to create a huge volume of parts in a shorter quantity of time compared to conventional stamping methods. This enhanced efficiency not just permits makers to meet tight manufacturing deadlines however additionally enables expense financial savings with economies of scale. In addition, high-speed marking can aid reduce material waste by optimizing the product usage during the marking process.
In addition, high-speed stamping strategies often include innovative features such as quick die change systems and real-time surveillance capacities, additionally boosting the overall performance and adaptability of the metal marking process. As innovation remains to breakthrough, high-speed stamping is anticipated to play an essential duty in driving the future of accuracy manufacturing.
Quality Assurance in Stamping Operations
Reliable quality control actions are vital for making sure the integrity and uniformity of metal marking operations. Quality assurance in marking procedures includes a series of organized procedures focused on finding and avoiding flaws in the made components. One critical aspect of quality This Site assurance in steel stamping is the usage of advanced examination strategies such as optical evaluation systems and coordinate determining equipments (CMMs) to confirm the measurements and tolerances of stamped components.
Furthermore, quality assurance steps in marking procedures commonly include the implementation of statistical process control (copyright) methods to keep track of the manufacturing process in real-time and make sure that it continues to be within appropriate restrictions. By assessing information and determining fads, manufacturers can proactively address any type of inconsistencies from the wanted top quality standards.
Moreover, quality control in metal marking operations additionally involves extensive material testing to make sure that the raw materials made use of meet the needed specs for the stamping procedure. This may include carrying out material firmness examinations, tensile strength tests, and dimensional examinations to ensure the quality and stability of the stamped components. In general, implementing robust quality assurance actions is critical for accomplishing top notch stamped parts continually.
Conclusion
To conclude, progressed strategies in metal stamping play a crucial duty in accuracy production processes. Via multi-stage marking processes, ingenious tooling services, automation, high-speed strategies, and rigorous top quality control measures, suppliers can accomplish higher degrees of accuracy and performance in read review their procedures. These innovations in metal marking technology have actually allowed business to create complex components with tight tolerances, inevitably resulting in improved product quality and customer complete satisfaction in the manufacturing industry.